As a startup, when you’re trying to stay as lean as possible, outsourcing is the name of the game; if you can get someone else to do the work for you (and manage the team, deal with hiring and HR, etc.), that’s a win. The major exception is anything that creates core intellectual property and technology, and things that are absolutely mission-critical to the business. It turns out for ButcherBox, a company that’s shipping hundreds of thousands of boxes of meat, dry ice is one of those things.
“During COVID, we ended up opening a dry ice factory, and we’ve now opened a second,” said Mike Salguero, CEO at ButcherBox, during a talk at the Baukunst Creative Technologist conference in Boston last week.
There were a few macro-economic reasons for why that suddenly started making sense. The first was that in 2020, the administration passed a law that made it advantageous to finance certain types of equipment.
“We bought these machines for $2 million each, on a five-year note, with 0% interest, and we were able to deduct it all in year one,” Salguero said, shaking his head. The tax and financial benefits were huge in a world where ButcherBox was making a lot of profit (the company did in excess of $440 million worth of revenue in 2021), directly related to COVID. “It was basically free. It’s like Trump paid us to buy these machines.”
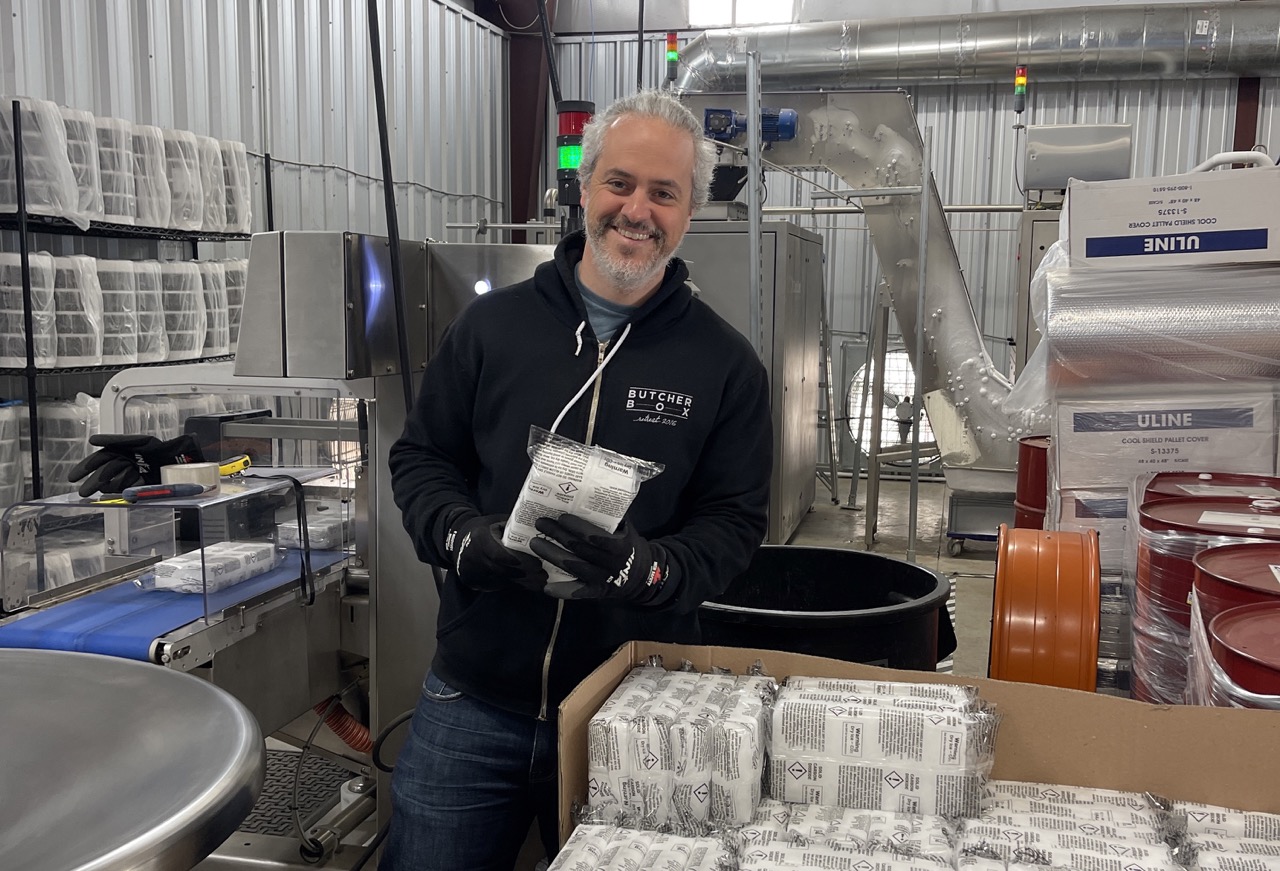
Mike Salguero at ButcherBox’s dry ice factory. Image Credits: ButcherBox
The purchase made sense financially, but it also de-risked a hugely important part of the business.
“What we do is frozen meat in the mail, which means we need dry ice. If we don’t have dry ice, we can’t ship,” Salguero said, suggesting that dry ice was the only thing that was truly mission-critical in his supply chain. “If we ran out of boxes, we could get different boxes. If we ran out of chicken breasts, we could like substitute for whatever, chicken thighs or turkey. If we run out of dry ice, we can’t ship, and we’re dead.”
Especially in 2020 as the pandemic was gathering steam, this looked like a bigger and bigger risk. There was a vaccine on the way that would need a lot of dry ice to get shipped around the country, and a lot of other businesses were starting to ship as well.
“We thought that that was going to get worse, and these machines were like really cheap for the amount of dry ice they could produce. Now we own our destiny as it relates to dry ice. The plant is only just coming online, but we will actually be sellers of dry ice,” says Salguero. “The real dream is that we can run these plants and make our own dry ice free because we are selling so much of it.”
The first factory in Oklahoma City, opened in the summer of 2021, can make an average of 111,000 pounds of dry ice every day. A second plant in Muscatine, Iowa is spooling up as we speak.
Why ButcherBox built two dry ice factories during the pandemic by Haje Jan Kamps originally published on TechCrunch